Technology 01
Vacuum metalized foil technology
Accumulation of specialized technology acquired as a specialized manufacturer
What we are proud of is the stability during transfer, which is the most important requirement for stamping foils. We lead the industry in technology that continuously produces foils in high speed with stable quality, and achieve outstanding yields.
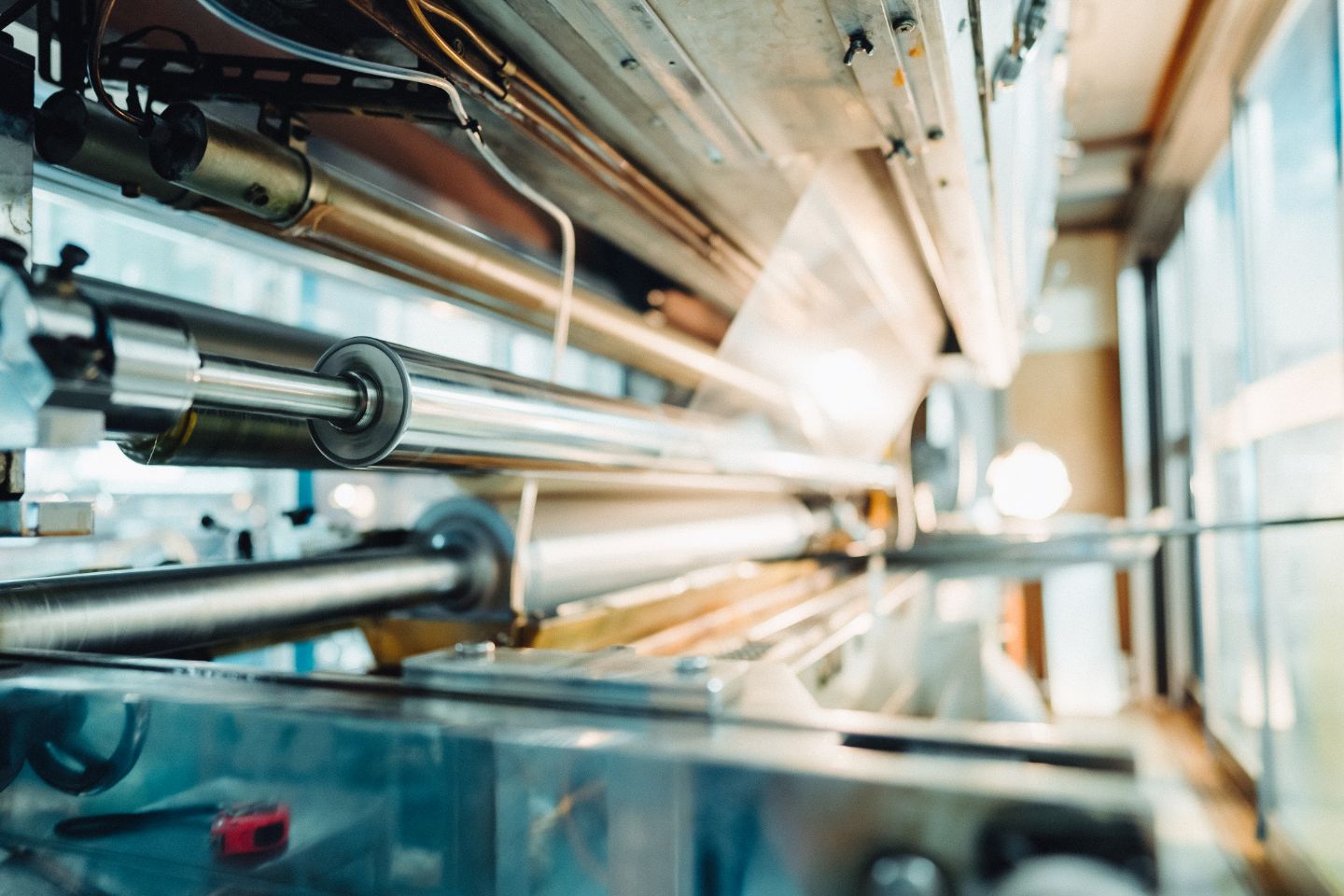
Features of the technology
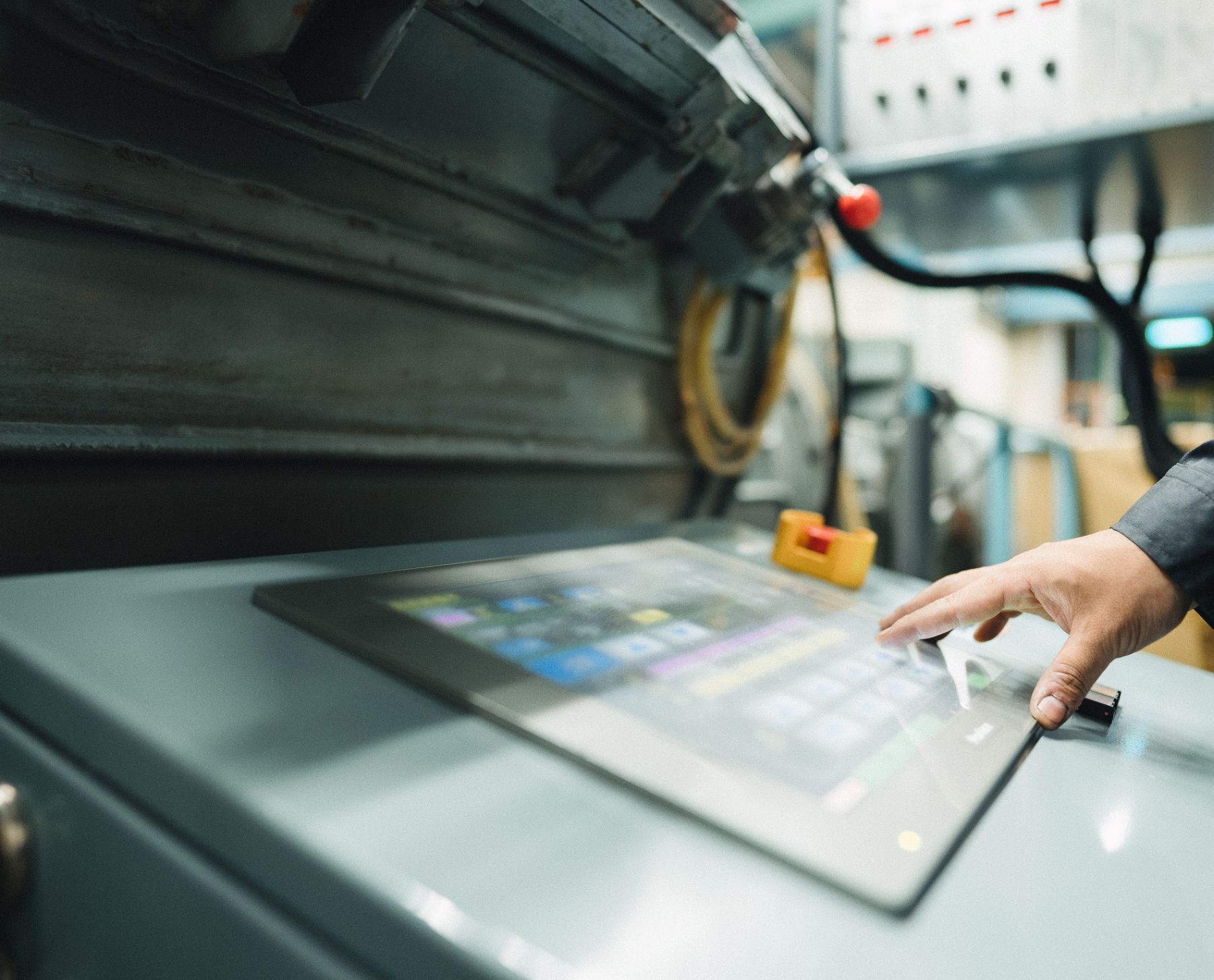
We focus on each step of the process and create the optimal design
In order to achieve the quality required by customers, we carefully examine and manufacture each product.
Just as a top chef flexibly changes recipes based on the foodstuffs available, we use our outstanding technologies and knowledge to create high quality foils for any substrate. We have established strict quality control standards for each work process, and have built a unique total quality control system that organically handles each process.
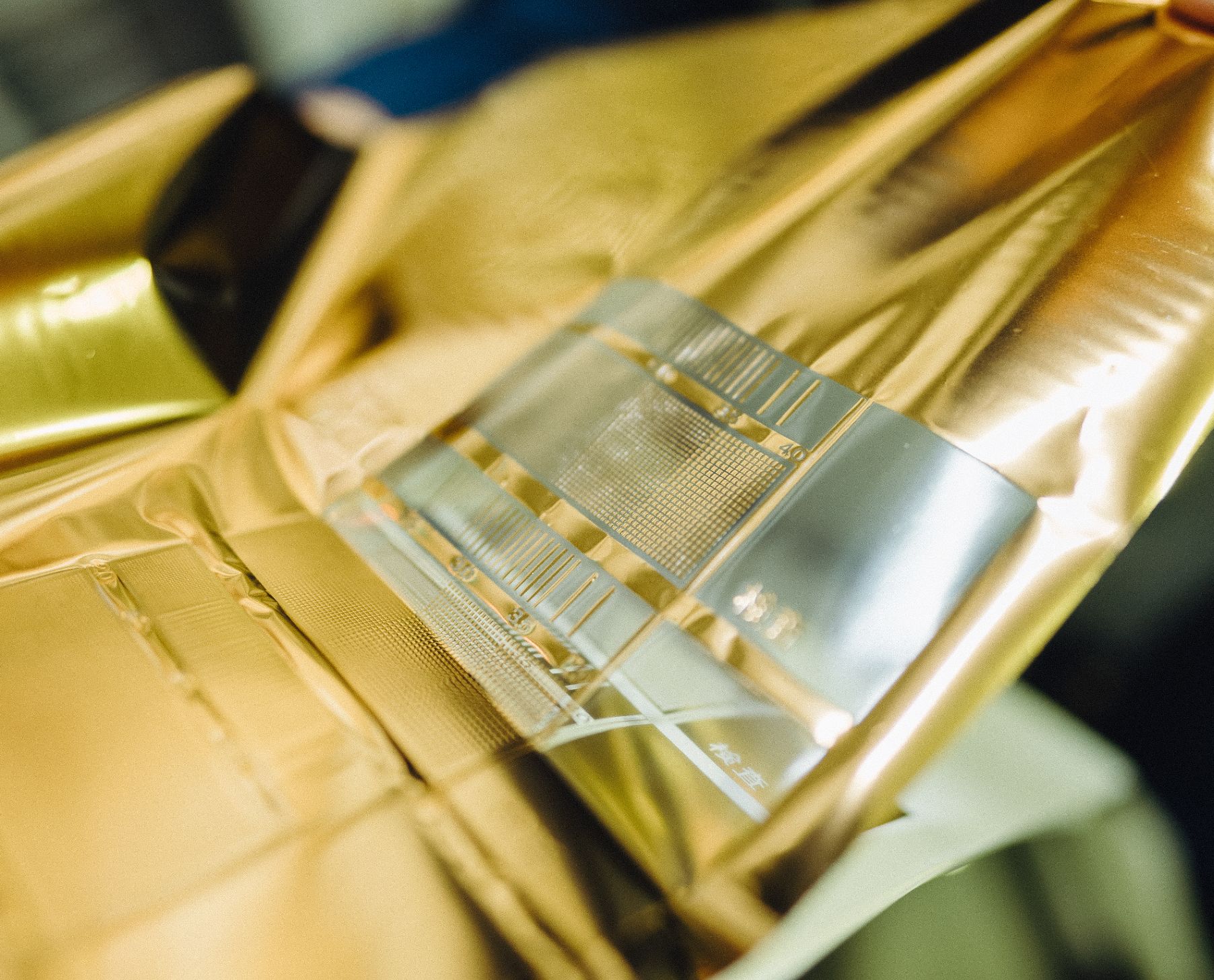
High performance "edge cutting property" and "releasability"
There are several standards that describe the performance of foils. One is the "edge cutting property". If a foil is cut finely, you can stamp small letters clearly. Another one is the "releasability" when releasing a stamping foil after stamping. If a foil is cut finely, it will become heavier when released, and its running speed will normally slower.
We maintain the highest standards in both "edge cutting property" and "releasability", so our foils exhibit excellent processing performance, and this allows for a speedy and beautiful finish.
If a foil is cut finely it will become heavier when it is released and its running speed will normally slower."
If a foil is finely cut, it will become heavier when released, and its running speed will usually be slower."
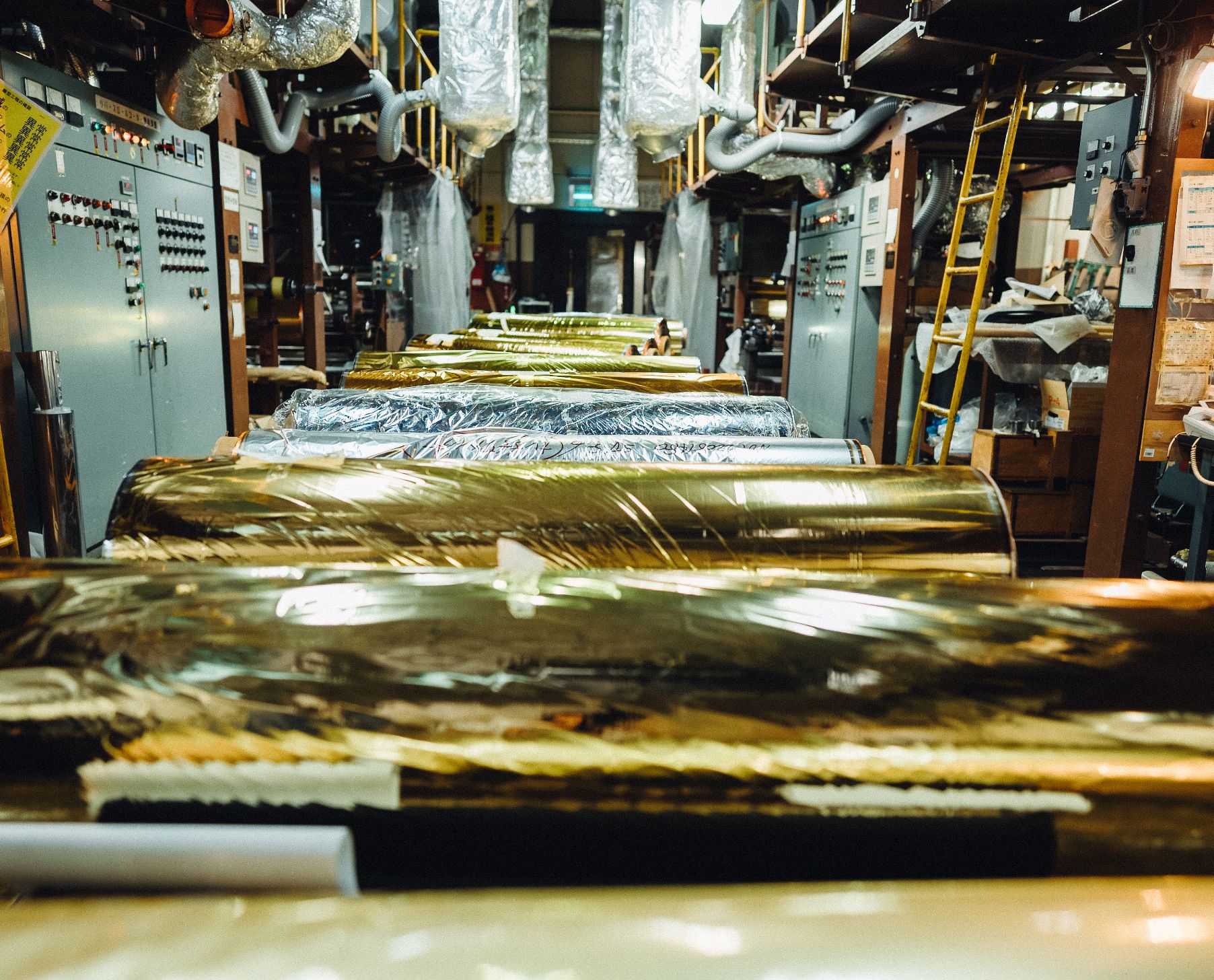
No color variation and no production lot variation
Our products do not have any color variation, and there is no variation in quality among different production lots. During manufacturing, products are greatly influenced by the environment, such as seasonal temperature and humidity difference. If you always use the same manufacturing way without thinking, the quality will vary.
By continually making improvements based on feedback from various evaluations on a daily basis, we have acquired technologies that allow us to achieve constant qualities in any season or environment. This allows our customers to have access to the same quality foil all year round.
Production process
-
01
Release layer
This layer has the function of peeling off the transfer layer from the surface of a carrier film. After transfer, it peels off from the film and acts as a protective layer, contributing to improved abrasion resistance.
-
02
Colored layer
This layer has design and functionality. This is applied by a gravure coater, etc., heated, and dried to form the layer. The colored layer consists of resins, dyes, or pigments. The shade is not only toned to the specified color, but the layer also acts as a protective layer that determines the physical properties (heat resistance, light resistance, abrasion resistance, etc.) of foils.
-
03
Vacuum metalized layer
Metal such as aluminum is deposited on the colored layer. Vacuum metallization gives a foil a glittering effect, further enhancing its decorative effect. In the vacuum evaporation method, aluminum molecules are deposited from the evaporation source and condense on the object to be deposited to form a layer, but the working conditions when forming this affect the quality of the layer.
-
04
Adhesive layer
This is applied onto the aluminum layer by a gravure coater or reverse coater, and then heated and dried to form the layer. Adhesives are selected from basic resins having good adhesion properties depending on the substrate to be stamped, and designed with tackifiers, pigments, solvents, etc.
-
05
Slitter / Winding inspection
Finished products are slit to shipping sizes and re-winded. Each product is strictly inspected to ensure that it passes the specified inspection items.
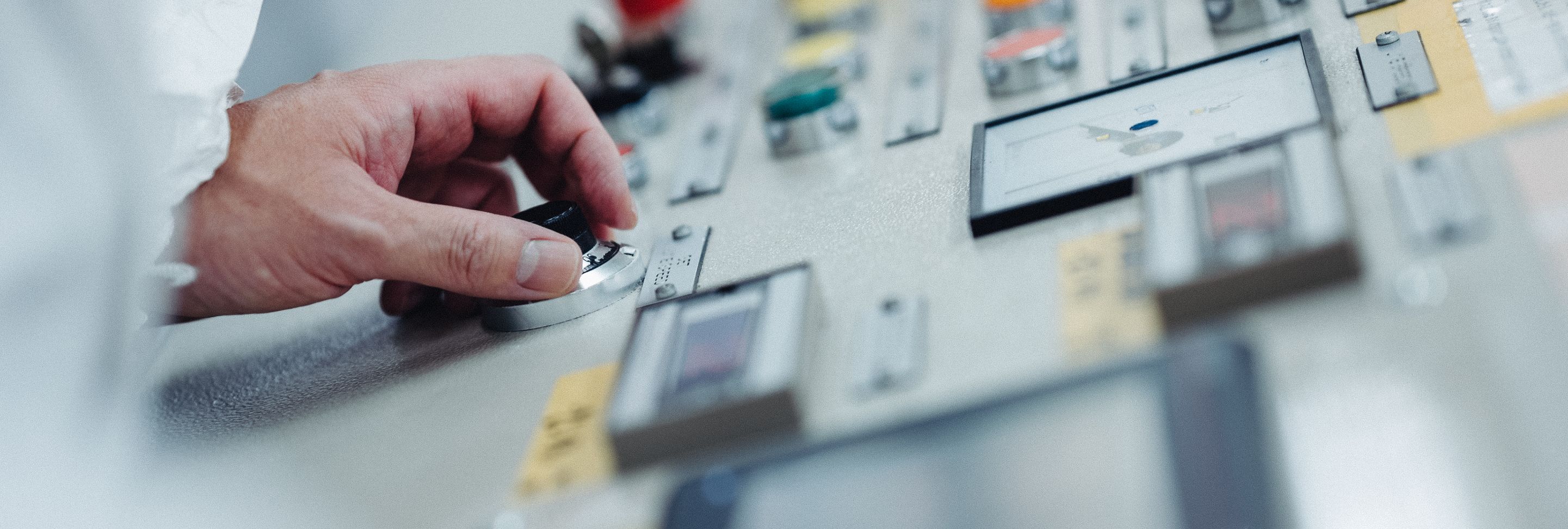